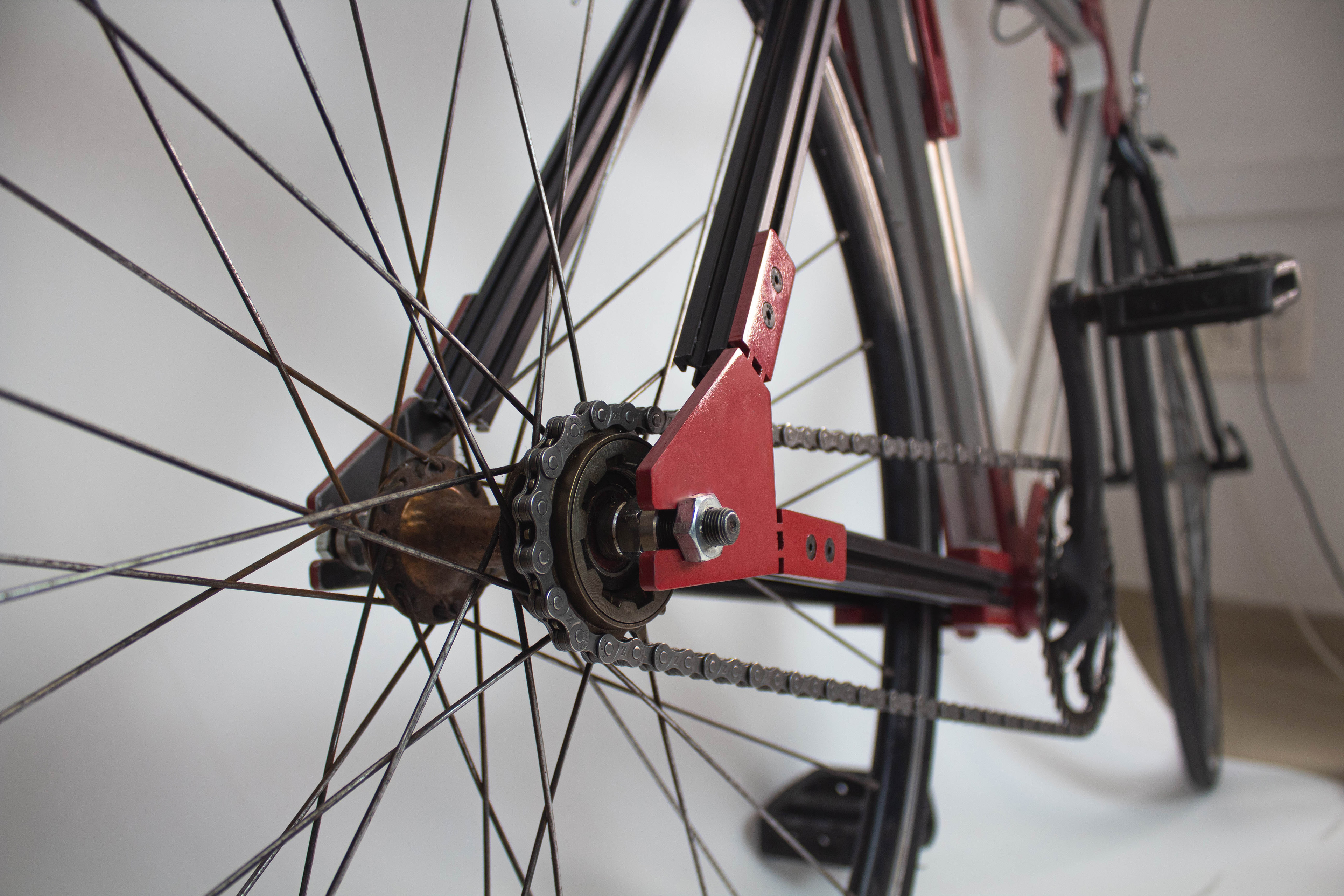
The Challenge
In this course, teams were tasked with creating a bike frame from scratch.
Our approach considered production, global shipping, and customization. We chose to use aluminum extrusions, known as "Sima" profiles in Israel, to design a flat-packable bike that could be customized for each rider, allowing users to attach personal accessories. What seemed like a simple idea presented a significant mechanical challenge.
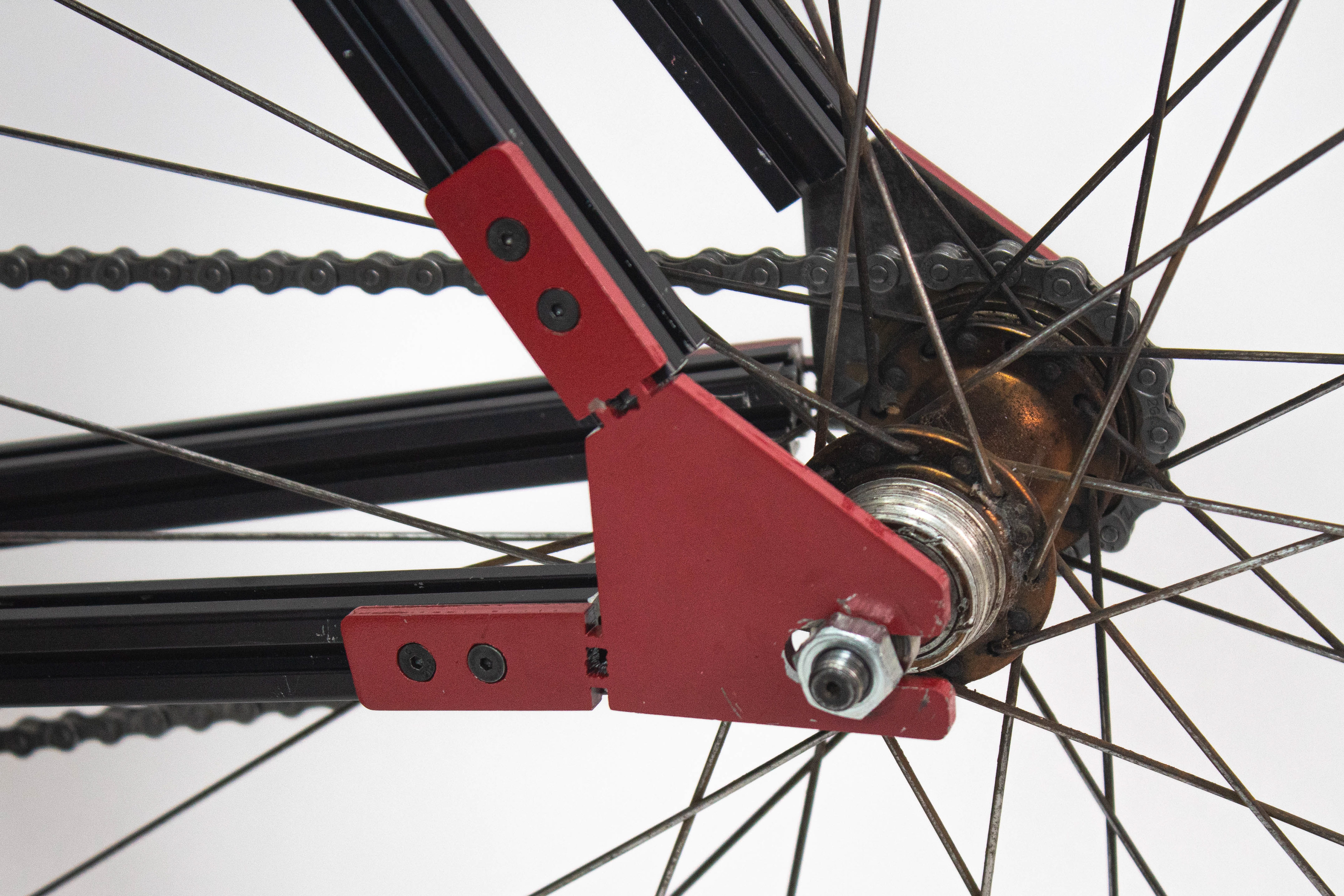
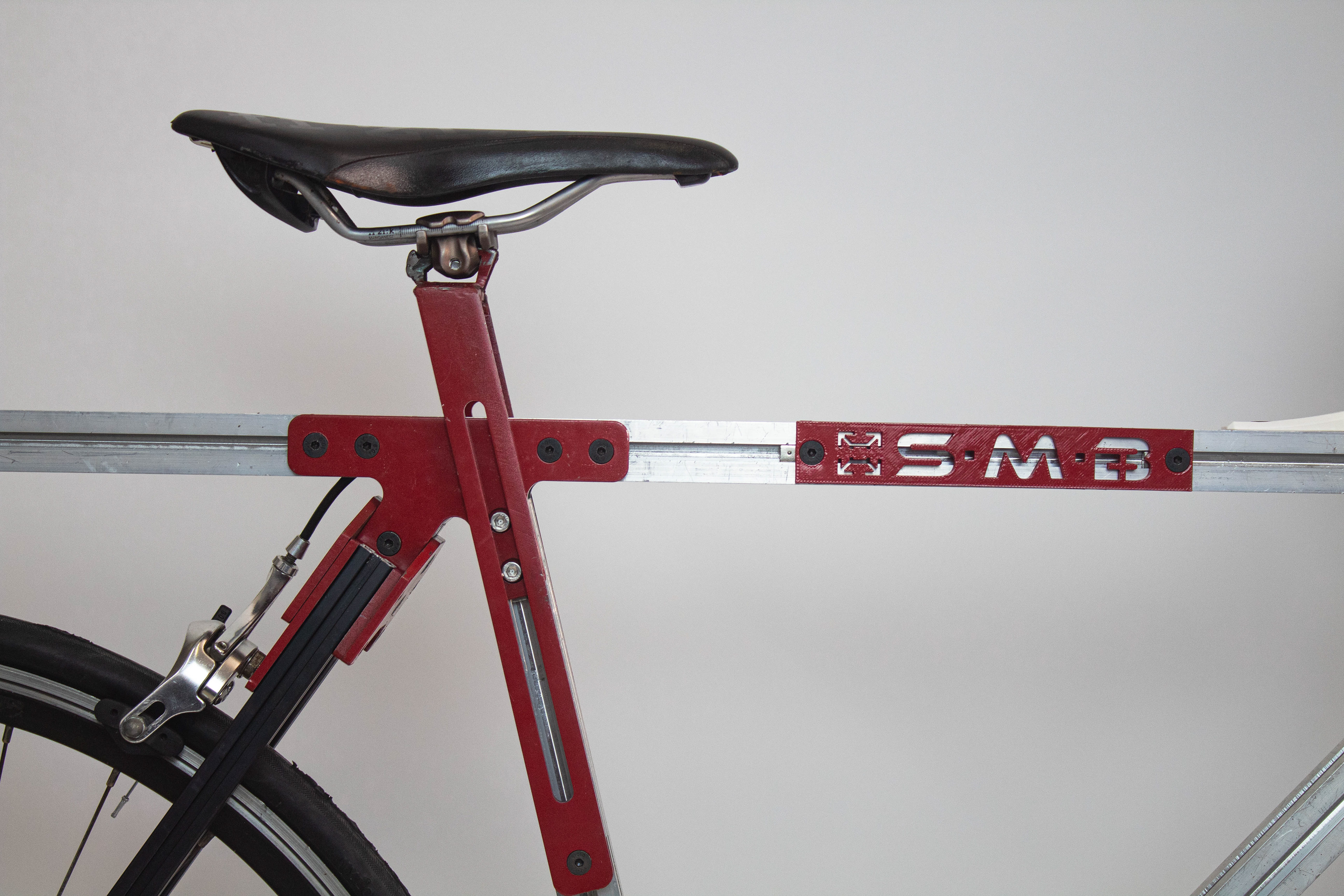
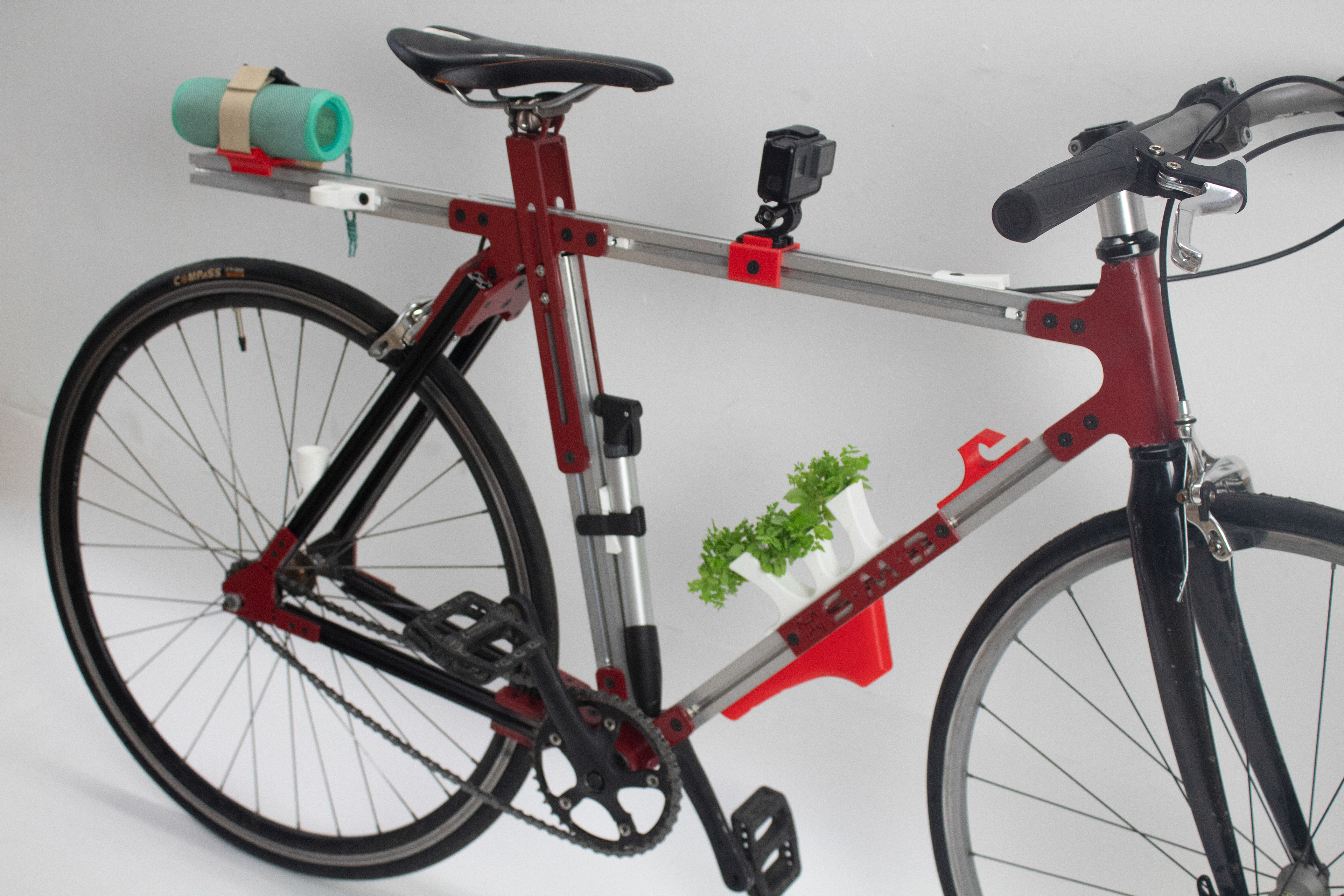
The process
At first we tested out 3D printing with nylon filament as a form of connection, there were some very interesting design problem to be dealt with and the direction was promising.
Parallel to the prints we prototyped laser cut connectors. The two dimensional approach was a great success and when compared to 3d printing which took a lot longer we decided on Laser cut sheet metal as the way to go.
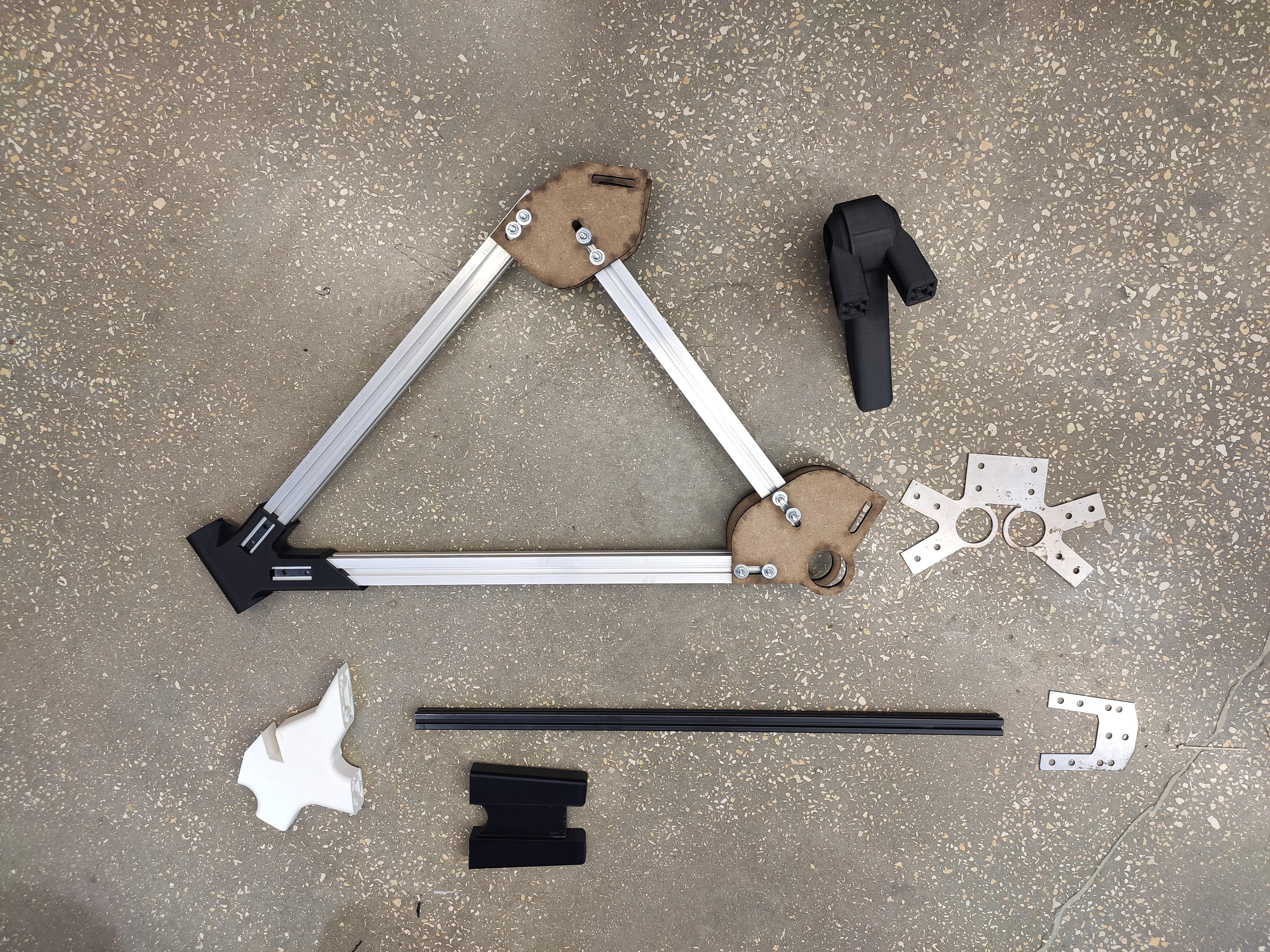
Now came the hard part, getting everything just right.
The months that followed were filled with testing and failing and repeating. Getting the angles and lengths correct, connecting a square profile with the circular one that holds the seat (with two dimensional sheet metal) and how to get the wheels aligned perfectly.
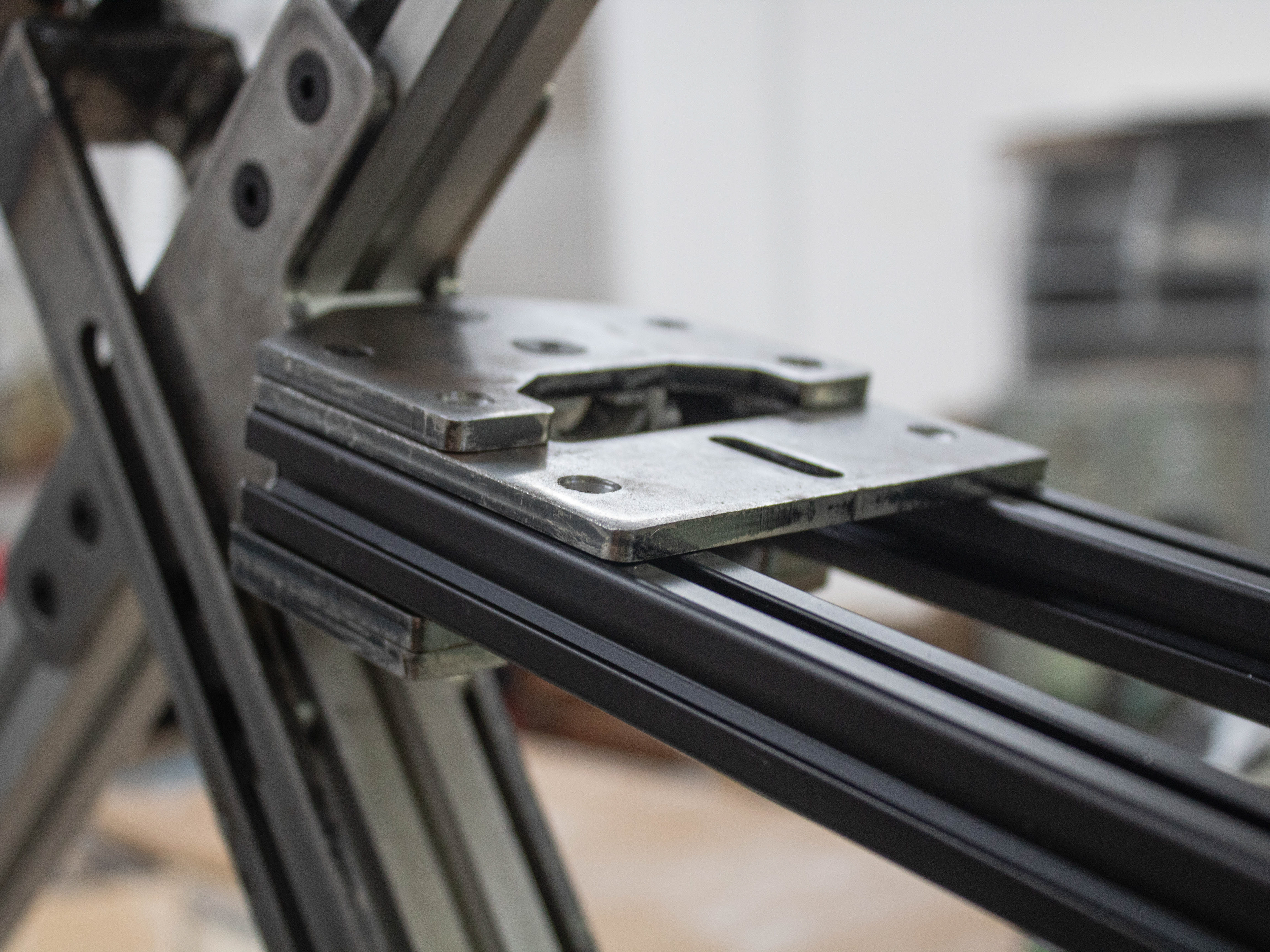
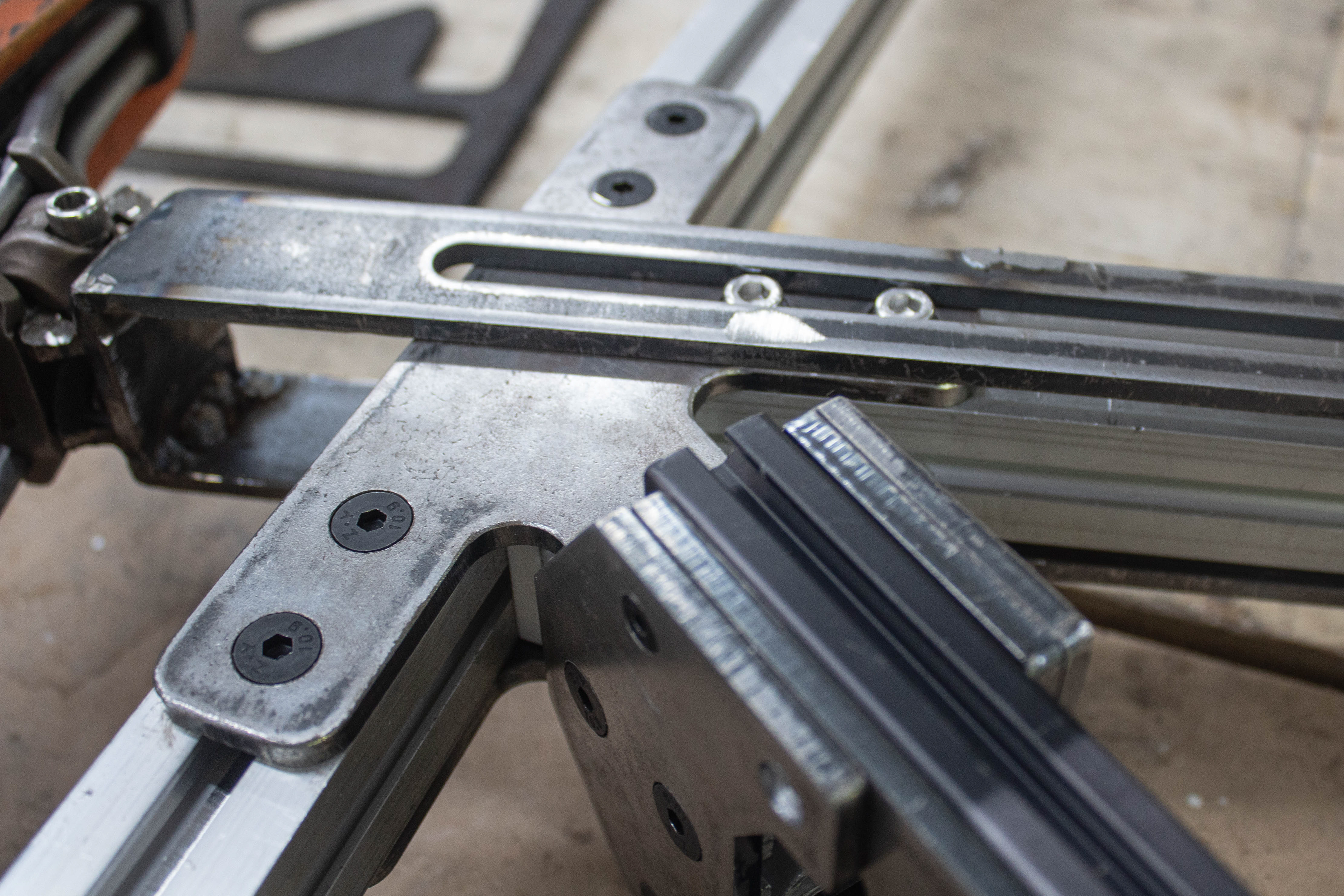
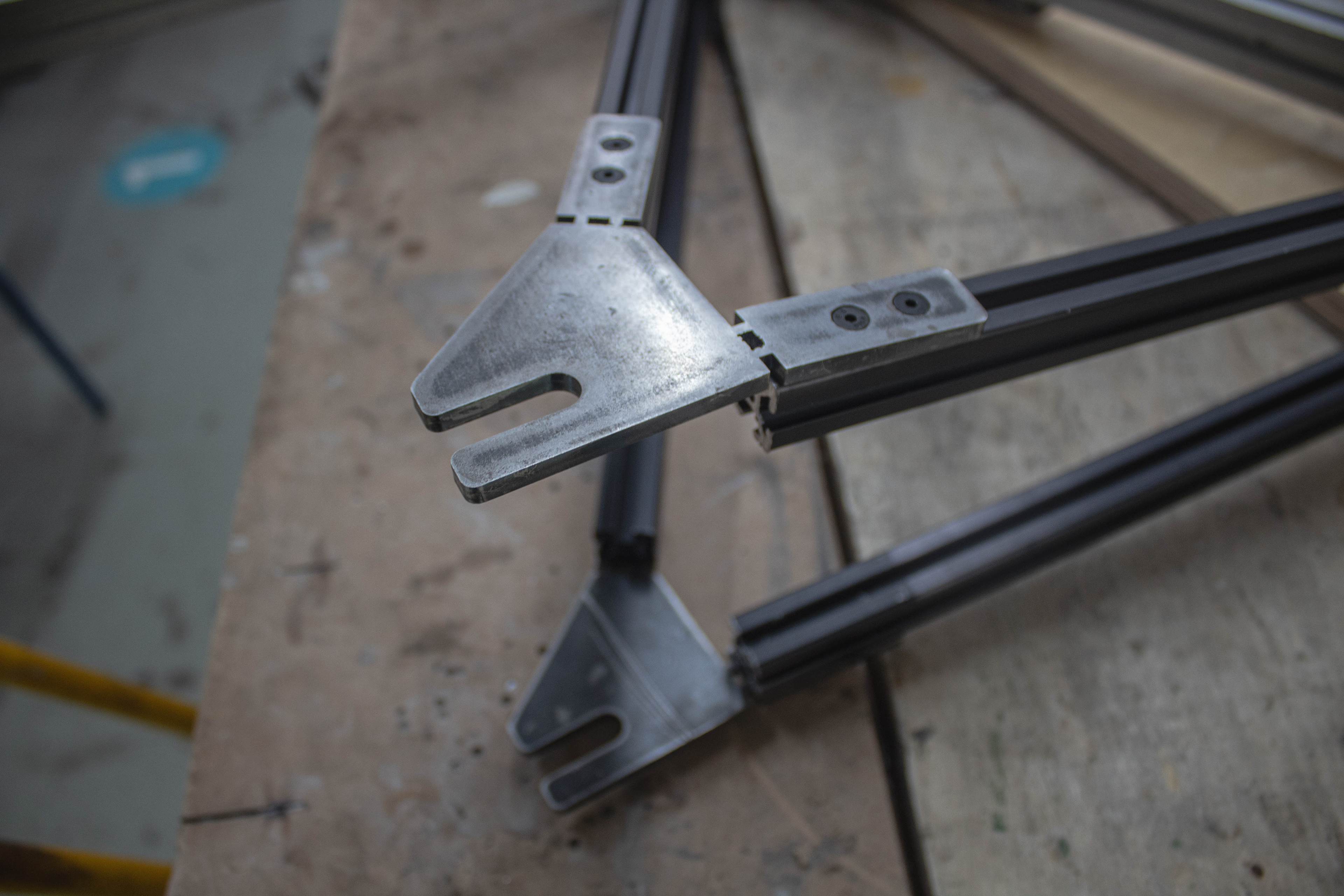
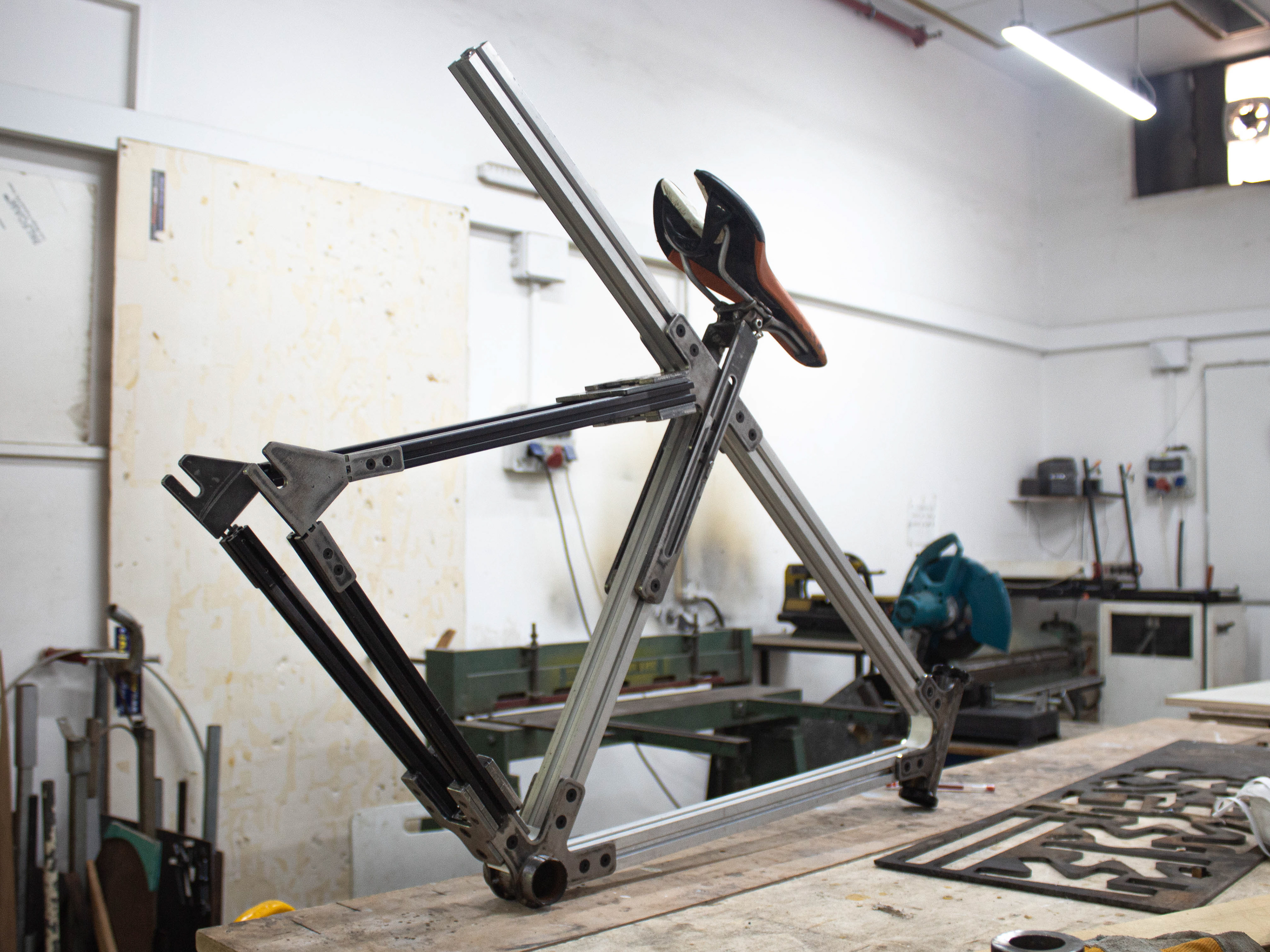
Everything needed to build the frame in one picture. Not in the image - the two Allen keys that are used for the assembly (yes, that's all that is needed).
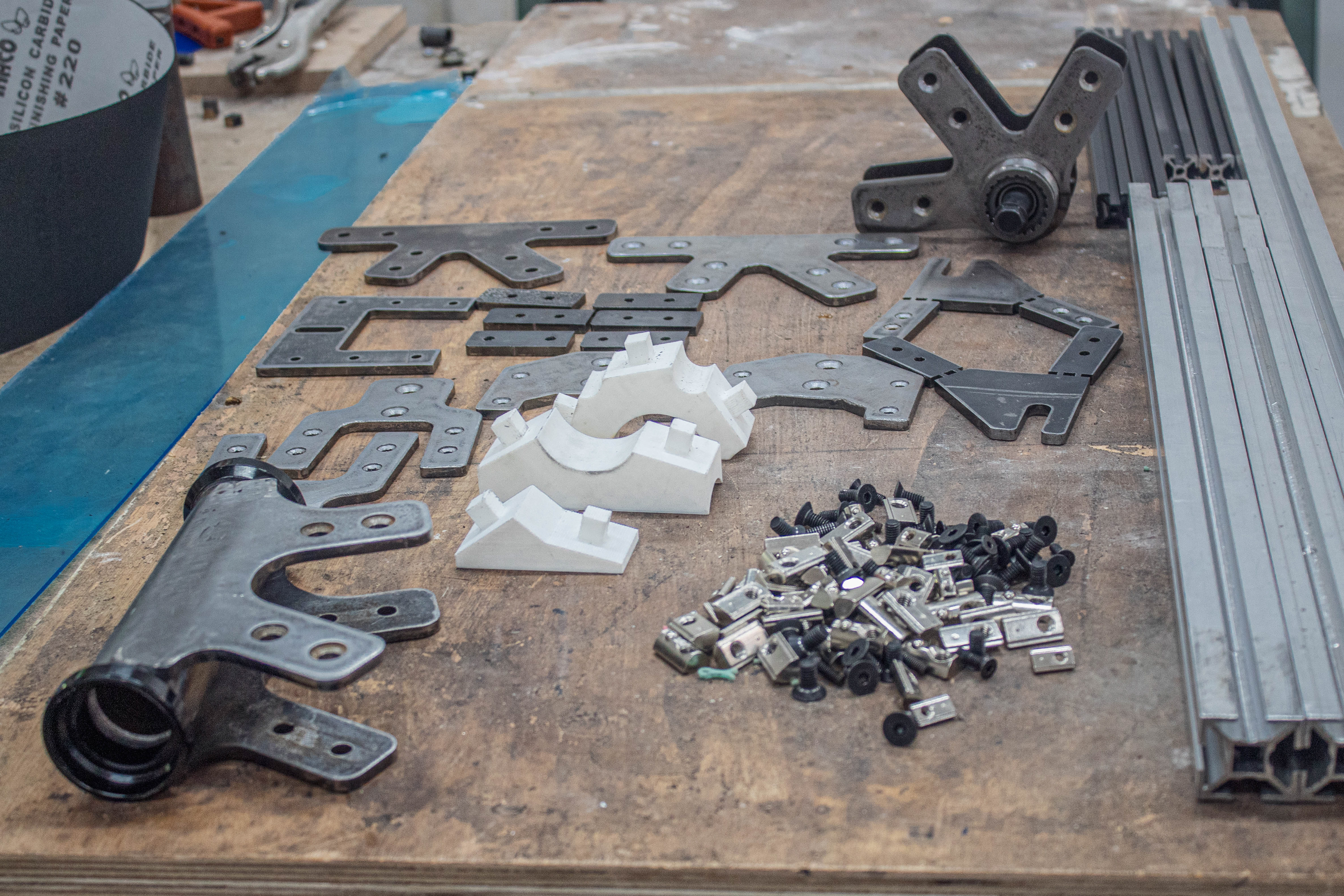
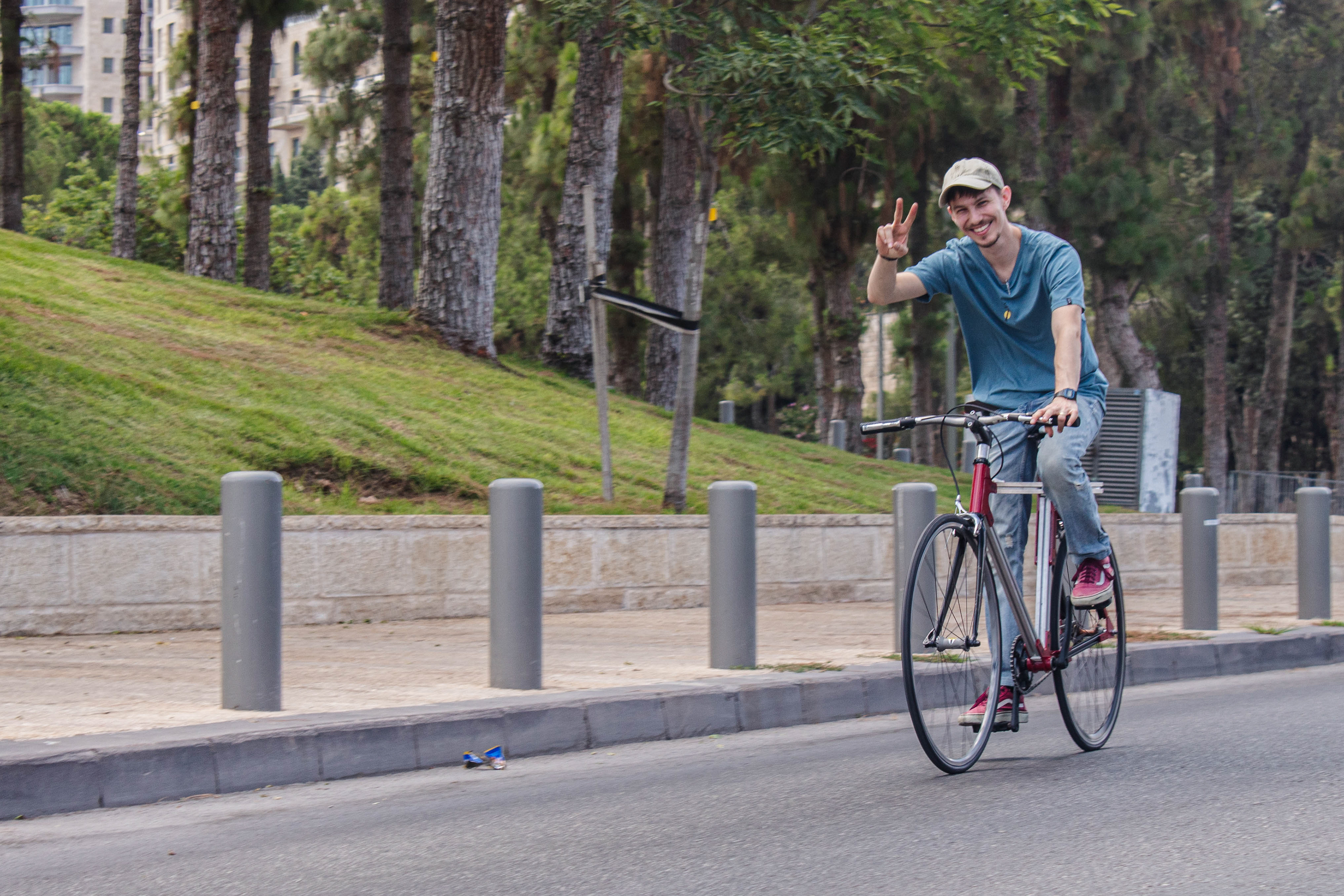